반도체 칩이 ON/OFF 스위칭의 전기적 신호를 빠른 속도로 처리하려면 막을 얇고 균일하게, 시간 변수에도 오래 버틸 수 있도록 형성해야 합니다. 반도체 트랜지스터를 만들 때에는 막을 쌓는 일부터 시작하는데요. 막을 형성하는 방법으로는 증착(Deposition), 회전(Spin On Glass), 전해도금(Electroplating) 등이 있습니다. 이중에서 가장 많이 쓰이는 증착은 물리적 기상증착방법(PVD, Physical Vapor Deposition)과 화학적 기상증착방법(CVD, Chemical Vapor Deposition)으로 크게 나뉩니다. 현재 반도체 공정에서는 CVD를 많이 사용하고 있는데요. 이는 PVD보다 표면접착력이 10배 높고, 대부분의 표면에 적용 가능하므로 활용도가 더 높기 때문이지요. 앞서 반도체 특강에서는 PVD 방식과 CVD 방식 중, 원자를 이용해 박막을 만드는 ALD에 대해 알아보았는데요. 오늘은 CVD 방식 중에서도 많이 보편화되어 있는 플라즈마 CVD(PECVD)와 고밀도플라즈마 증착(HDPCVD) 등을 중심으로 살펴보도록 하겠습니다.
CVD 방식의 종류
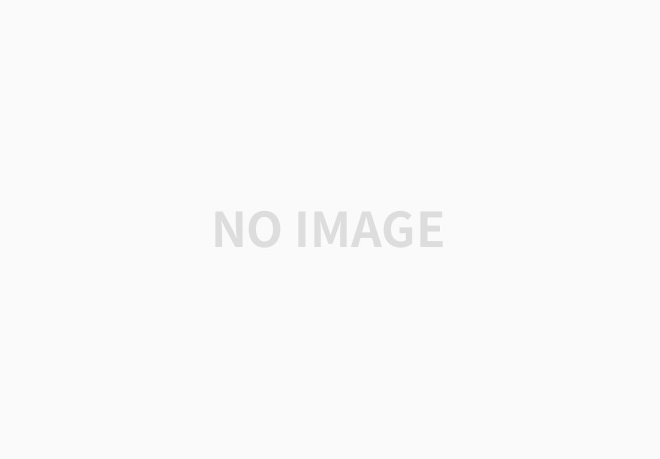
▲ CVD 방식의 종류
증착(Deposition)은 반도체 공정 중에서도 가장 다양한 방식으로 이루어져 있습니다. 증착막을 만들 때에는 증기(Vapor)를 이용하는데, 대표적인 방법으로 물리적 기상증착방법(PVD, Physical Vapor Deposition)과 화학적 기상증착방법(CVD, Chemical Vapor Deposition)이 있습니다. 이번 편에서 살펴볼 CVD는 프로세스 챔버 속 원료기체의 원소가 화학적으로 다른 원소로 변하면서 웨이퍼 표면에 달라붙어 증착하는 방법입니다. CVD는 가장 오래된 반도체 공정 중 하나로써, 긴 역사만큼 많은 진화를 거쳐왔다고 볼 수 있는데요. 열에너지를 이용한 방식으로는 APCVD(대기압 Atmosphere pressure CVD)와 LPCVD(저기압 Low Pressure CVD)가 있고, 플라즈마 에너지를 이용한 방식으로는 PECVD(저밀도 플라즈마)와 HDPCVD(고밀도 플라즈마)가 있습니다. 최근에는 원자를 표면에 흡착시키는 방식으로 한층 한층씩 쌓아 올리는 원자층 증착방법(ALCVD)을 많이 적용하는 추세입니다.
CVD의 세 가지 요소
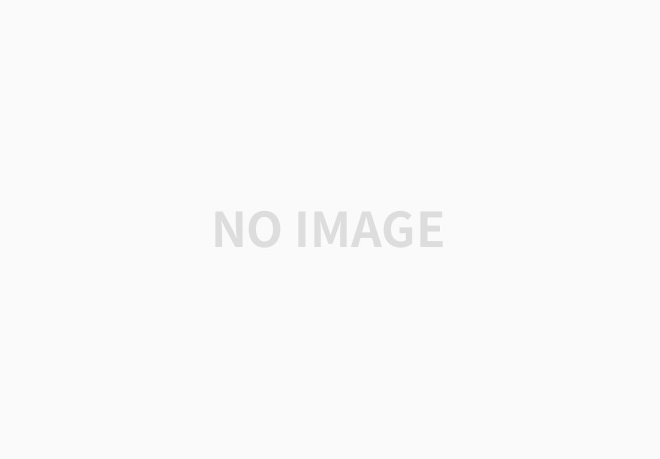
▲ CVD 3요소
CVD는 원료기체 가스들이 화학 반응을 거쳐 고체 상태(막)로 변하는 공정입니다. 단순히 물리적 상태(고체 →기체 →고체)만을 변화시켜 막을 만드는 PVD에 비해, CVD는 뜨거운 웨이퍼 표면에서 가스가 반응하여 원래의 기체 원소와는 최종적으로 다른 화학적 조성을 갖게 됩니다. CVD공정의 핵심요소로는 진공압력, 온도 및 화학적 원소라 할 수 있으며 챔버를 제어하는 요소로는 부피 변화를 포함한 진공압력과 온도와의 상관관계입니다. CVD는 막의 두께는 얇게, 막의 밀도는 높이는 방향으로 진행되는데, 그에 따라 작업을 진행하는 프로세스 챔버 속에는 특별한 환경이 조성되어야 합니다. 여기서 중요한 것은 진공을 얼마나 낮은 압력으로 만들 수 있느냐, 또 막의 위치와 공정 진행 방식에 따라 어떤 에너지를 얼마큼 투입해 가스를 활성화할 것이냐 입니다.
진공을 만든다
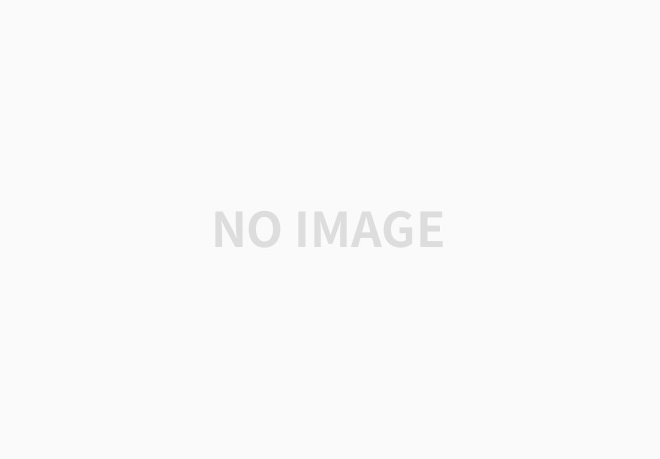
▲ 압력을 기준으로 본 CVD
증착은 대부분 진공상태에서 진행하는데, 그 중 CVD는 초기에 대기압(APCVD) 상태에서 진행되었습니다. 이후 대기압의 절반 정도 수준인 준기압(SACVD: Semi-APCVD)을 적용했다가, 최종적으로 프로세스 챔버 내 기압을 대기압의 약 100분의 1 정도까지 낮추게 되었지요. 진공도가 높아지면 가스 분자끼리의 충돌이 적어지고, 그에 따라 기체 확산이 활발해져 APCVD에 비해 더욱 정밀하고 균일한 필름(얇은 막)을 만들 수 있습니다. 저압 상태일수록 막을 성장시킬 때 트랜치나 Gap 혹은 Hole의 측벽면증착이 잘 되고(단차피복성: Step Coverage), 막 전체의 두께가 일정(두께균일성: Uniformity)해집니다. 이것들은 CVD공정능력을 가늠하는 잣대가 되기도 하지요. 그런데 문제는 압력이 낮을수록 공정의 프로세싱 시간이 길어진다는 것입니다. 따라서 공정시간을 단축하는 것이 관건인데요(CVD의 대표주자였던 APCVD는 초창기에 많이 사용했습니다만, 8인치 웨이퍼를 사용하면서 줄어들면서 12인치에서는 Uniformity 문제로 인하여 거의 적용하지 않습니다). 고진공 상태에서 기체들의 반응 속도를 떨어뜨리지 않으려면 웨이퍼 온도를 높여야 합니다.
온도를 높인다, 그러나 높일 수 없다
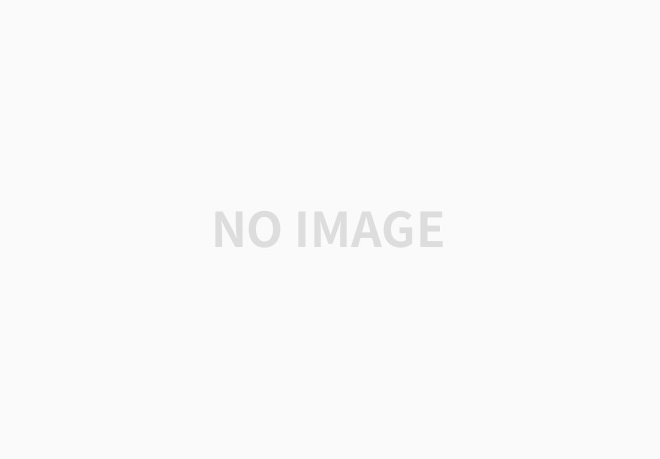
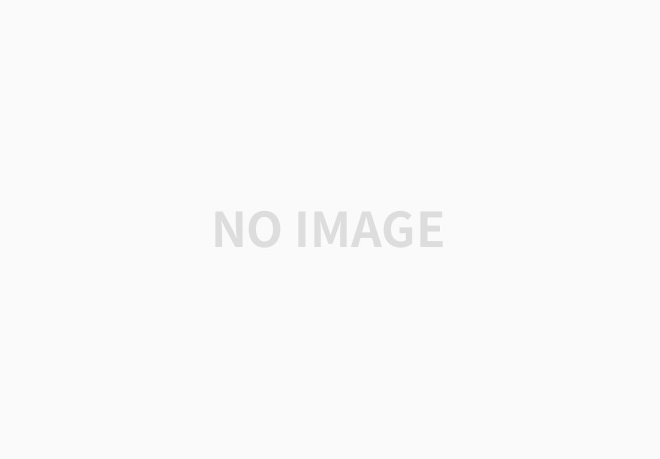
▲ 온도를 기준으로 본 CVD 증착막
두 종류 이상의 원료기체 원소들을 결합시켜 증착막을 만들려면 많은 에너지가 투입되어야 합니다. 열에너지를 이용한 CVD는 압력이 낮아질 때 증착률이 감소하므로, 웨이퍼 온도를 높여 화학적 반응을 활발하게 합니다(APCVD에서 LPCVD 방식으로 가면서 압력을 100분의 1배로 줄이는 반면, 온도를 2배로 증가시킵니다. 그렇다고 LPCVD가 APCVD보다 증착 속도가 빨라지는 것은 아니지만, 진공으로 고품질의 막질을 얻을 수 있다는 장점이 있습니다). Poly Gate막 혹은 Gate Oxide 절연막과 같은 하부막은 그 밑에 별다른 막이 없으므로 LPCVD를 진행하면서 웨이퍼 온도를 섭씨 1,000도 가까이 높여도 하부에 녹는 막이 없습니다. 하지만 IMD(Inter-Metal Dielectric)층 같은 트랜지스터 상부에 위치한 막을 LPCVD의 온도(섭씨 1,000도)로 진행할 경우, 그 밑에 있는 메탈층(Word Line)이 녹아 내리는 불상사가 발생합니다. 따라서 낮은 온도에서도 단차피복성과 막의 균일성 등을 LPCVD와 비슷하게 형성할 수 있도록 플라즈마CVD(PECVD)가 개발되었습니다. PECVD는 열에너지를 적게 사용하는 대신 플라즈마 에너지를 보충하여 증착시키는 방식입니다.
플라즈마 증착(PECVD)
메탈층이 1~2개였던 1990년대 초반까지만 해도 집적도가 낮았기 때문에 APCVD 등을 적용할 수 있었습니다. 낮은 온도에서도 다소 거친 막질로 메탈층을 보호할 수 있었지요. 하지만 최근에는 특히 하부막으로 메탈층(알루미늄, 구리 등)이 여러 개 늘어났으며, 또 메탈과 메탈 사이 간격이 좁아져 절연막(IMD)으로 채워주어야 합니다. 이 경우 하부막인 메탈이 녹지 않도록 반드시 저온 공정인 PECVD나 HDPCVD를 적용해야 합니다. 상부에 위치한 Passivation보호막도 마찬가지입니다.
PECVD는 플라즈마를 만들 때 생성된 여러 가지 입자(양이온, 음이온, 전자, 라디칼 등) 중 라디칼(Radical)을 이용합니다. 라디칼은 에너지적으로 볼 때 매우 불안정하여 저온(섭씨 약 400도)에서도 다른 원소와 화학적으로 쉽게 결합하는데요. 저온임에도 불구하고 증착 속도는 빠르지만, 막질 상태가 좋지 않고 라디칼의 이방성(한쪽 방향으로만 진행) 성질로 인하여 Step Coverage가 발생한다는 단점이 있습니다. 따라서 막의 품질이 좀 떨어져도 무방한 위치에만 한정적으로 사용합니다.
고밀도플라즈마 증착(HDPCVD)
이러한 PECVD의 단점을 보완하기 위해 개발된 것이 바로 고밀도플라즈마(HDPCVD)입니다. 증착 속도는 PECVD보다 느리지만 치밀한 막질을 얻을 수 있는 방법이지요. 챔버 내는 백만 분의 1기압 정도로 유지합니다. 증착하면서 발생되는 스퍼터(Sputter)식각 시에 아르곤 이온의 직진성을 확보해주면 증착할 공간이 충분히 확보됩니다. 이렇게 되면 증착 후에 형성되는 증착막 내의 void도 거의 생기지 않게 됩니다. 이는 트랜치 혹은 Gap을 채우는 데에도 탁월한 효과가 있어서 SOG(Spin On Glass)를 대체할 뿐 아니라, 최근에는 PECVD의 대부분이 HDPCVD로 바뀌어가는 추세입니다.
웨이퍼 형태를 변형시키는 Fab 공정 중, 증착은 가장 변수가 많고 다양한 방법을 활용할 수 있는 공정입니다. 그만큼 노하우가 많이 쌓여있어 우리나라의 가장 경쟁력 있는 공정 중 하나이기도 하지요. 특히 오늘 살펴본 CVD는 트랜지스터 막을 구성하는 데 있어 비약적인 발전을 이룬 기술입니다. 현재 개발된 어느 공정보다도 가장 얇고 순도 높은 막을 어떠한 형태로든 균일하게 생성해낼 수 있지요. 따라서 향후, 다양성과 발전 가능성이 매우 높은 공정이라고 볼 수 있습니다.
'정리하는 반도체 > 반도체 공정' 카테고리의 다른 글
EUV Lithography (0) | 2020.05.30 |
---|---|
게이트와 커패시턴스 (0) | 2020.05.27 |
반도체 세정공정 (0) | 2020.05.23 |
리소그래피(Lithography) (0) | 2020.05.22 |
이온-임플란테이션 후 어닐링(Annealing) (0) | 2020.05.21 |